1. СОСТАВ БЕТОННЫХ
И ЖЕЛЕЗОБЕТОННЫХ РАБОТ
Большинство сооружений систем водоснабжения
и водоотведения возводится из бетонных и железобетонных
конструкций. В зависимости от способа производства
работ различают конструкции монолитные, сборные и
сборно-монолитные с ненапрягаемой и напрягаемой арматурой. Источник статьи: www.sbh.ru
В состав бетонных и железобетонных
работ входят заготовительные, транспортные
и монтажно-укладочные процессы. Заготовительные процессы
включают в себя изготовление опалубки,
арматуры, или их блоков, подача и распределение смеси,
ее укладка и уплотнение, выдерживание бетона и уход
за ним, распалубливание и отделка конструкций. Блок-схема
комплексного процесса производства бетонных работ
представлена на рис. 13.1.
2. ОПАЛУБОЧНЫЕ И АРМАТУРНЫЕ
РАБОТЫ
Опалубка
предназначена для придания возводимым конструкциям
проектной формы, заданных размеров и положения в пространстве.
В опалубку укладывают бетонную смесь и выдерживают
ее в ней до достижения распалубочной прочности. По
материалам формирующей поверхности различают опалубку
деревянную, металлическую,
железобетонную, армоцементную, из синтетических материалов
(пластмассовая опалубка) и прорезиненных тканей. По
условиям применения опалубку подразделяют на инвентарную,
т.е. многократно используемую, и стационарную, используемую
только для одного сооружения.
По конструкции и назначению инвентарная
опалубка может быть разборно-переставной, переставной,
скользящей, катучей и несъемной. Опалубку всех типов
изготовляют из различных материалов и их комбинаций.
Опалубка может выполняться греющей
и утепленной (термоопалубка).
Разборно-переставная опалубка
бывает мелко- и крупнощитовая, а также объемная (блочная).
Мелкощитовая
опалубка состоит из отдельных шитов небольшого размера
(до 1 м2) и
массы (до 50 кг), а также несущих и поддерживающих
элементов, крепежных и соединительных узлов.
Крупнощитовая
опалубка состоит из крупноразмерных щитов (массой
более 50 кг), элементов их соединений и крепления.
Щиты этой опалубки воспринимают все технологические
нагрузки без применения дополнительных несущих и поддерживающих
конструкций. Они включают в себя палубу, элементы
жесткости и несущие детали, оборудованы подмостями
для бетонирования, подкосами и анкерами для установки.
Объемно-переставная опалубка
состоит из секций, образующих в рабочем положении
опалубку П-образной формы для бетонирования стен и
перекрытий. Объемно-переставная опалубка используется
для бетонирования коллекторов и тоннелей, блочная
опалубка может состоять как из отдельных щитов, так
и из специально изготовленных блоков. Она включает
в себя опалубку для бетонирования ступенчатых фундаментов,
ростверков (блок-формы). Применяют также крупноразмерные,
арматурно-опалубочные блоки. Разновидностью переставной
опалубки является пневматическая (надувная) опалубка
из прорезиненных и других специальных тканей. Она
применяется для бетонирования купольных и сводчатых
покрытий. При нагнетании воздуха оболочка опалубки
приобретает заданную форму, а по достижении бетоном
распалубочной прочности воздух из нее выпускают и
конструкцию освобождают от опалубки.
Рис. 13.2. Виды катучей горизонтально
и вертикально скользящей опалубки (а,б,в,г), несъемной
(д,е) и греющей опалубки (ж):
1 - тележки; 2 - щиты опалубки; 3 - бетонируемая
конструкция; 4 - каркас; 5 - катки; 6 - поперечина;
7 - отверстия для болтов; 8 - рама наружной опалубки;
9 - опорная доска; 10 - стойка с домкратом; 11
- рама; 12, 13 - верхние и боковые щиты; 14 -
рычаги; 15 - опорная наружная рама; 16 - подъемная
внутренняя рама; 17 - привод винтового подъема;
18 - винт; 19, 20 - ригели подъемной опорной рамы;
21 - кружала; 22 - опорные пластины; 23 - короба;
24 - напорные рукава; 25 - подвесные леса; 26
- козырек; 27 - гидравлический домкрат; 28 - настил
рабочей площадки; 29 - внутренние подвесные подмости;
30 - греющий кабель; 31 - крепление кабеля; 32
- утеплитель; 33 - защитный кожух; 34 - вырез
для крепления щитов; 35 - вилочный разъем щитов |
Статья подготовлена и представлена в цифровом виде
компанией "SBH COTPAHC"
Катучая опалубка
применяется для бетонирования стен (рис. 13.2, а)
и тоннелей коллекторов (рис. 13.2, б). Рама опалубки
установлена на катках для перемещения вдоль бетонируемых
конструкций. Внутренняя опалубка для прямоугольных
коллекторов и тоннелей может раздвигаться на разные
размеры по высоте и ширине. Ее устанавливают и распалубливают
с помощью винтового домкрата. Разновидностью катучей
опалубки является горизонтально-скользящая конструкция,
используемая для бетонирования прямо- и криволинейных
стен сооружений.
Вертикально-скользящая опалубка
(см. рис. 13.2, г) состоит из щитов, закрепленных
на домкратных рамах, рабочего пола, домкратов и приводных
станций. Вся система опирается на домкратные стержни,
заделанные в бетон через 1,5-2 м по периметру стен,
и поднимается по мере их возведения домкратами. Применяют
такую опалубку для возведения стен высотных сооружений
типа водонапорных башен, градирен высотой 40-50 м
и более. Преимуществами такой опалубки являются: значительная
оборачиваемость (до 50 раз и более), высокое качество
и прочность бетонируемых конструкций вследствие непрерывной
укладки смеси. Одним из ее недостатков является необходимость
использования домкратных стержней. Более эффективной
является новая конструкция бесстержневой подъемно-скользящей
опалубки (см. рис. 13.2, в), подъемный механизм которой
опирается на затвердевший бетон нижерасположенной
возведенной стены. Подъем опалубки обеспечивается
двухсекционным подъемным механизмом шагающего действия. Источник статьи: www.sbh.ru
Несъемная опалубка
устраивается из ребристых (рис. 13.2, д) или гладких
железобетонных плит (рис. 13.2, е); применяют также
армо- и стеклоцементные плиты, пластмассовые и асбестоцементные
листы, реже металл. Она выполняет одновременно две
функции: опалубки при бетонировании и защитной облицовки.
Плиты имеют размеры 1 х 4 м и толщину 50—60 мм. Для
лучшего сцепления с бетоном их делают с шероховатой
поверхностью или снабжают анкерующими петлями-выпусками.
Ребристые опалубочные плиты изготавливают шириной
0,6 м или 1,2 м и длиной до 6 м. Применяют несъемную
опалубку-облицовку при бетонировании массивных фундаментов,
стен толщиной более 0,5 м, опускных колодцев и т.п.
Греющая опалубка
(рис. 13.2, ж) включает в себя греющие элементы, из
которых наиболее удобны в применении электрические
нагреватели. Для увеличения долговечности, т.е. оборачиваемости
инвентарной опалубки и повышения качества поверхности
бетонируемых конструкций применяют меры по уменьшению
сил сцепления опалубки с бетоном. С этой целью используют
различные гидрофобизи-рующие, т.е. водоотталкивающие
смазки, эмульсии, а также различные покрытия, особенно
из полимеров (пластмассовая опалубка). Они почти полностью
устраняют сцепление, не загрязняют бетон и выдерживают
до 30 циклов оборачиваемости.
Сборку опалубки
или ее монтаж ведут, как правило, из готовых элементов
(щитов, панелей) и узлов крепления, изготовленных
в опалубочных мастерских или цехах.
Качество опалубки
должно удовлетворять требованиям ГОСТа и СНиПа. Конструкции
опалубки, поддерживающих лесов, а также стоек и крепежных
деталей должны обеспечивать прочность, жесткость и
устойчивость при укладке бетона, легкость установки
и разборки.
Монтаж арматуры.
Для армирования железобетонных конструкций применяют
стержневую, проволочную арматуру и арматурные изделия.
Конструкции армируют как отдельными стержнями, так
и укрупненными арматурными изделиями — сетками и пространственными
каркасами. По назначению арматура подразделяется на
рабочую (расчетную), распределительную (конструктивную),
монтажную и хомуты.
Применение арматурно-опалубочных блоков позволяет
значительно ускорить арматурно-опалубочные работы.
Их изготавливают из готовых пространственных самонесущих
арматурных каркасов и оснащают опалубкой и подмостями.
До установки каркасов и арматурно-опалубочных блоков
в проектное положение выправляют и выверяют арматурные
выпуски ранее забетонированной конструкции и наводят
разбивочные оси. Арматурные каркасы монтируют самоходными
кранами с применением специальных траверс (рис. 13.3,
а). Каркасы фундаментов и подколенников большой массы
при высоте их более 2 м устанавливают краном с использованием
самобалансирующихся стропов (рис. 13.3, б). Монтаж
арматурно-опалубочных блоков также осуществляют краном
(рис. 13.3, в) и установку его начинают с разметки
осевых линий, после чего к верху каждой стороны блока
крепят инвентарные рас-
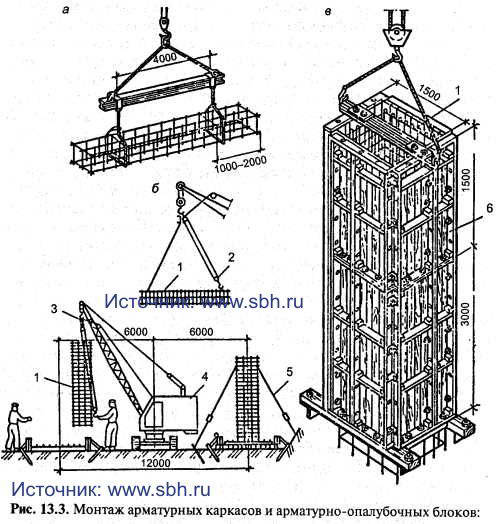
Рис. 13.3. Монтаж арматурных каркасов и арматурно-опалубочных
блоков:
1 — каркас; 2 — блок вспомогательного крюка; 3
— полуавтоматический строп; 4 — кран; 5 — расчалка;
6 — щитовая опалубка |
чалки и стропят к крюку самобалансирующейся траверсой.
Подняв блок, его разворачивают и наводят так, чтобы
осевые риски на нем и на основании или фундаменте
совпали. Блок опускают, проверяют положение осей и
вертикальность установки, после чего закрепляют расчалки.
Сварка арматуры
при ее монтаже. Для соединения арматурных стержней,
сеток и каркасов применяют различные виды сварки.
Электродуговая сварка, основанная на принципе
образования электрической дуги между свариваемыми
стержнями и электродом, применяется при изготовлении
арматурных каркасов из стержней диаметром 8-80 мм
(внахлест и с накладками). Однако этот способ неэкономичен,
так как вызывает значительный расход металла на накладки.
Ванная и ванношовная сварка являются
разновидностью электродуговой. При их использовании
стержни с необходимым зазором укладывают в стальную
или медную желобчатую форму, а в зазор вставляют гребенку
электродов. При прохождении тока между формой и электродами
возникает дуга и образуется ванна расплавленного металла,
который плавит торцы стержней и сваривает их. Применяют
эти виды сварки для соединения стержней больших диаметров
непосредственно на месте установки арматуры. Контактная
сварка, или сварка сопротивлением, заключается
в том, что при прохождении электрического тока металл
в месте контакта стержней плавится и сваривает их.
Разновидностью ее является контактно-точечная и контактно-сты
ко рая сварки. Первая используется при изготовлении
сеток и плоских каркасов (для сварки пересечений стержней),
а вторая — для наращивания арматурных стержней из
горячекатаной стали. Это самый экономичный способ
сварки арматуры, так как не требует дополнительного
расхода металла на электроды, накладки и подкладки.
Полуавтоматическая сварка под слоем флюса
является также весьма экономичной и распространенной
на практике, особенно при соединении стержней больших
диаметров. Для такой сварки применяют медные или графитовые
разъемные формы, а также медные съемные накладки.
После из установки в зазор между стержнями засыпают
небольшое количество флюса и производят сварку стержней
электродной проволокой. Соединения вертикальных и
горизонтальных стержней арматуры диаметром 20-40 мм
выполняют полуавтоматической сваркой открытой дугой.
Особенности устройства предварительно
напряженной арматуры. При устройстве предварительно
напряженных железобетонных конструкпий применяют два
способа натяжения арматуры: на упо- 1 ры, т.е. до
бетонирования конструкции, и на бетон (после его затвердения).
Заготовка стержней напрягаемой арматуры заключается
в правке, чистке и отрезке стержней заданного размера,
в образовании на их концах анкеров или в установке
инвентарных зажимов. Сборку арматурных элементов в
пакеты с их выравниванием, высадку анкеров или установку
зажимов выполняют на постах заготовки арматуры. После
установки напрягаемой арматуры краном Е формы или
стенды и закрепления приступают к ее натяжению механическим,
электротермическим или электротермомеханичес-ким способом.
Предварительное
напряжение арматуры резервуаров, радиальных отстойников
и других цилиндрических сооружений чаше всего выполняют
двумя способами: 1) навивкой на стену высокопрочной
арматурной проволоки периодического профиля диаметром
3—5 мм с помощью навивочной машины; 2) установкой
колец из стержневой арматуры (класса A-IV) с последующим
натяжением ее электротермическим способом. Навивку
напряженной арматуры на стены сооружений осуществляют
специальными машинами типа АНМ (рис. 13.4, а), причем
сверху вниз непрерывной спиралью. Напряжение ее обеспечивается
вследствие разности скоростей движения тележки машин
и соответственно навивочного устройства (рис. 13.4,
б) v1, и
сматывания арматуры v2,
когда v2
< v1,.
Скорость навивки для машин АНМ различных марок 60-120
м/мин. Степень натяжения проволоки регулируется специальными
коническими барабанами и контролируется динамометром.
При многослойной навивке каждый последующий ряд арматуры
навивают после приобретения защитным торкрет-ным покрытием
предыдущего слоя прочности не менее 5 МПа. Сила натяжения
арматуры не должна отличаться от указанной в проекте
больше чем на ±10 %. На рис. 13.4, в показан процесс
навивки напряженной арматуры машиной АНМ-7, с помошью
которой можно навивать высокопрочную арматуру и проволоку
диаметром до 5 мм на стены сооружений диаметром от
16 до 70 м и высотой до 12 м. Электротермический способ
натяжения арматуры основан на том принципе, что стержни
при прохождении по ним электрического тока нагреваются
и удлиняются, если их в таком виде закрепить на упорах,
то после остывания они получат определенную величину
предварительного напряжения. Температура нагрева стержней
не должна превышать 400°С. При остывании стержни передают
сжимающие напряжения на стены сооружения.
Статья подготовлена и представлена в цифровом виде
компанией "SBH COTPAHC"
3. ВИДЫ БЕТОННЫХ СМЕСЕЙ
И СПОСОБЫ ИХ ПРИГОТОВЛЕНИЯ
Комплексный технологический
процесс бетонирования конструкций, как это видно из
блок-схемы на рис. 13.1, включает приготовление бетонной
смеси и транспортирования ее на строящийся объект,
подачу, распределение, укладку и уплотнение ее в конструкции,
уход за бетоном в процессе твердения.
К бетонной смеси предъявляются два основных требования:
1) при транспортировании, перегрузке и укладке в опалубку
она должна сохранять однородность; 2) обладать удобоукладываемостью.
Однородность смеси обеспечивается связностью (нерасслаиваемостью)
и водоудерживающей способностью, которые достигаются
правильным подбором состава смеси, точностью дозировки
составляющих и тщательным их перемешиванием. Удобоукладываемость
смеси зависит от ее зернового состава и количества
воды, которые назначаются в зависимости от характера
и размеров бетонируемых конструкций, степени армирования,
способов транспортирования и уплотнения смеси. Чтобы
отвечать этим требованиям, смесь должна иметь определенную
консистенцию, которая в зависимости от условий укладки
ее может изменяться от жидкой до густой и жесткой.
Уровень этой консистенции определяют с помощью стандартного
конуса и вискозиметра. Если осадка конуса до 2 см
смесь считается жесткой, если 4— 6 см — смесь малоподвижная,
если 8-12 - подвижная, если 14-18 - высоко подвижная
и, наконец, если осадка конуса превышает 18 см — смесь
литая.
Рис. 13.4. Навивка предварительно напряженной
кольцевой арматуры на стены цилиндрических сооружений:
1 — ось вращения; 2 — стрела; 3 — бухтодержатель;
4 — лебедка; 5 — стена сооружения; 6 — верхняя
тележка; 7 — вертикальная рама; В — нижняя тележка;
9 — цепь; 10 — приводная звездочка; 11 — конический
барабан; 12 — механизм торможения; 13 — катки
тележки; 14 — подвесная (нижняя) тележка с на-вивочным
устройством; 15— напрягаемая арматура; 16 — направляющие
ролики; 17 — натяжное устройство; 18 — электродвигатель;
19 — станок для сращивания проволоки; 20 •— место
машиниста; 21 — стойка |
Бетонную смесь
готовят в соответствии с заданными по проекту маркой
(или как теперь принято классом) бетона по прочности
и с предъявляемыми к нему требованиями по водонепроницаемости,
морозостойкости, сохранению механических свойств в
агрессивных средах.
Удобоукладываемость
(жесткость) смеси определяется на техническом вискозиметре
и составляет: более 200 с - для особо жестких; 30-200
- для жестких; 15-30 - для малоподвижных смесей.
По прочности
на сжатие, согласно СНиПу, установлены следующие
классы тяжелых бетонов В3,5; B5; B7,5; BIO; B12,5;
B15; В20; В25; ВЗО; В35; В40; В45; B50; B55; В60.
Соотношение между
классами и марками приведено в табл. 13.1.
Таблица 13.1 Соотношение между классами бетона
по прочности на сжатие и марками
Класс бетона по
прочности (В) |
Средняя прочность
бетона данного класса МПа (кгс/см2)
|
Ближайшая марка
бетона по прочности (М) |
В3,5 |
4,6 (45,84) |
М50 |
В5 |
6,5 (65,48) |
М75 |
В7,5 |
9,8 (98,23) |
М100 |
В10 |
13,1 (130,97) |
М150 |
В12,5 |
16,4 (163,71) |
М150 |
В15 |
19,6 (196,45) |
М200 |
В20 |
26,2 (261,93) |
М250 |
В25 |
32,7 (327,42) |
М350 |
В30 |
39,3 (392,90) |
М400 |
В35 |
45,8 (458,39) |
М450 |
В40 |
52,4 (523,87) |
М550 |
В45 |
58,9 (589,35) |
М600 |
В50 |
65,5 (654,84) |
М700 |
В55 |
72,0 (720,32) |
М700 |
В60 |
78,6 (785,81) |
М800 |
По водонепроницаемости
установлены марки W2; W4; W8; W10; W12.
По морозостойкости
для тяжелого бетона установлены марки F50; F75; F100;
F150. Для напрягающего и мелкозернистого - F200; F300;
F400; F500. Для легкого бетона - F25; F35; F50; F100;
F150; F200; F300; F400; F500.
В строительном
производстве используют различные виды бетонов. Для
возведения сооружений систем водоснабжения и водоотве-дения
применяется в основном гидротехнический бетон, отличающийся
повышенными показателями по прочности, водонепроницаемости,
водо- и морозостойкости.
Процесс приготовления
бетонной смеси включает в себя операции по приему
и складированию составляющих материалов (цемента и
заполнителей), дозирования и перемешивания с водой,
а также выдачи готовой бетонной смеси на транспортные
средства.
Обычно бетонную
смесь приготовляют на централизованных бетонных заводах
или на приобъектных инвентарных (передвижных) бетоносмесительных
установках. Основными техническими средствами, смонтированными
на бетоносмесительных заводах и установках, являются
расходные бункеры с распределительный устройствами,
дозаторы, бетоносмесители, системы внутренних транспортных
средств и коммуникаций, раздаточный бункер. Указанное
технологическое оборудование может быть скомпоновано
по одноступенчатой (вертикальной, или башенной) и
двухступенчатой (партерной) схеме. При вертикальной,
или башенной схеме размещения оборудования (рис. 13.5,
а) составляющие материалы бетонной смеси (вяжущие,
заполнители, вода) поднимаются в верхнюю точку технологического
процесса один раз и далее перемещаются вниз под действием
собственной силы тяжести, а при партерной, те. двухступенчатой
(рис. 13.5, б) подъем происходит дважды. Наиболее
компактны и экономичны башенные установки, но из-за
значительной высоты (до 35 м) усложняется их монтаж.
Рис. 13.5. Схемы компоновки бетоносмесительных
заводов и установок:
а— одноступенчатая (вертикальная, или башенная);
б — двухступенчатая (партерная); 1 — конвейер
склада заполнителей; 2 — конвейер подачи заполни-телей
в расходные бункера; 3, 9, Ю— поворотная направляющая
и распределительная; 4 — расходные бункера; 5
— трубопровод пневмоподачи цемента; 6 — дозатор
цемента; 7 — дозатор заполнителей; 8 — дозатор
воды; 11 — бетоносмесители; 12 — раздаточный бункер
(копильник); 13 — автобетоновоз; 14 — автоцементовоз;
15 — скиповый подъемник |
Статья подготовлена и представлена в цифровом виде
компанией "SBH COTPAHC"
4. СПОСОБЫ ТРАНСПОРТИРОВАНИЯ,
УКЛАДКИ И УПЛОТНЕНИЯ БЕТОННОЙ СМЕСИ. ВЫДЕРЖИВАНИЕ
И УХОД ЗА БЕТОНОМ.
Транспортирование бетонной
смеси включает в себя доставку ее от места
приготовления на строительный объект, подачу смеси
непосредственно к месту укладки и распределения по
блоку бетонирования. При перевозке смесь должна быть
защищена от атмосферных осадков, замораживания, высушивания,
а также от вытекания цементного молока.
Допустимая продолжительность
перевозки зависит от температуры смеси при выходе
из смесителя: она не должна превышать 1 ч при температуре
20-30°С; 1,5 ч - 19-10°С; 2 ч - 9-5°С. Длительная
перевозка по плохим дорогам приводит к ее расслаиванию.
Поэтому в транспортных средствах без побуждения смеси
в пути не рекомендуется перевозить на расстояние больше
10 км по хорошим дорогам и больше 3 км - по плохим.
Для перевозки смеси
на объект широко применяют автомобильный транспорт
- автосамосвалы общего назначения, автобетоновозы
и автобетоносмесители (миксеры). Поскольку при перевозке
смеси автосамосвалами, широко применявшимися до недавнего
времени, возникают большие трудности по защите смеси
от замерзания, высушивания, утечки цементного молока
через щели в кузовах, а также по необходимости их
последующей ручной очистки, в последнее время все
чаще для перевозки бетонной смеси используют специализированные
автобетоновозы, оборудованные герметичными опрокидывающимися
кузовами мульдообразной формы. Ими стало возможно
перевозить смеси на расстояние до 25-30 км, причем
без расплески-вания ее и вытекания цементного молока.
Но наиболее эффективным средством транспортирования
являются автобетоносмесители, или миксеры, которые
загружаются на заводе сухими компонентами и в пути
следования или на стройплощадке приготавливают бетонную
смесь с осадкой конуса от 1 см и выше при температуре
окружающего воздуха не ниже 0°С. Выпускаются автобетоносмесители
вместимостью по готовому замесу от 3 до 10 м3.
Дальность перевозки сухих компонентов смеси в автобетоносмесителях
технологически не ограничена. Перемешивание их с водой
обычно начинается за 30—40 мин до прибытия на объект.
В автобетоносмесителях (миксерах) выгодно перевозить
также готовые бетонные смеси вследствие имеющейся
возможности их побуждения в пути за счет вращения
барабана. Источник статьи: www.sbh.ru
Доставленную на
объект смесь подают в бетонируемые конструкции кранами
в неповоротных или поворотных бадьях или ленточными
конвейерами (транспортерами), бетононасосами и пневмонагне-тателями
(по трубам), звеньевыми хоботами и виброхоботами,
ленточными бетоноукладчиками. Поворотные бадьи
вместимостью 0,5—8 м3
загружают непосредственно из самосвалов или бетоновозов,
причем при вместимости бадей 0,5 м3 - по четыре сразу
(рис. 13.6. а), а бадьи на 1,5...8 м3
загружают из бетоновозов, вместимость кузова которого
равна или кратна вместимости бадьи сразу (рис. 16.6,
б). Ленточные передвижные конвейеры применяют
в тех случаях, когда подать смесь к месту укладки
средствами доставки или в бадьях трудно или невозможно.
Конвейерами длиной до 15 м подают смесь на высоту
до 5,5 м. Чтобы уменьшить высоту свободного падения
смеси при выгрузке, применяют направляющие щитки или
воронки. Но конвейеры в процессе бетонирования необходимо
часто переставлять.
Рис. 13.6. Средства для подачи и распределения
бетонной смеси:
1 — бадьи при выгрузке смеси; 2 — полозья; 3 —
затвор; 4 — траверса; 5 — направляющие ковша;
6 —ковш; 7— вибробункер; 8 —конвейер; 9— поворотная
платформа; 10 — загрузочная воронка; 11 — смеситель;
12— электродвигатель; 13 — поршень; 14 — бетоновод;
15, 16 — нагнетательный и всасывающий клапаны |
Поэтому более эффективны в этом отношении самоходные
ленточные бетоноукладчики, смонтированные
на базе трактора (рис. 13.6, в), оборудованные скиповым
подъемником и ленточным конвейером длиной до 20 м.
Бетононасосы (рис. 13.6, г) применяют для
подачи смеси в любые виды конструкций, расположенных
в стесненных условиях и в местах, не доступных для
других средств транспорта. Промышленностью выпускаются
бетононасосы с механическим приводом с подачей 10
м3/ч и с гидравлическим
приводом на 20-30 м3/ч
при подаче ими смеси по стальному разъемному трубопроводу
(бетоноводу) на расстояние по горизонтали до 300 м
и по вертикали до 50 м. Пнев-монагнетатели также используют
для бесперегрузочной подачи смеси и ее укладки. Максимальная
дальность транспортирования смеси составляет 200 м
по горизонтали или до 35 м по вертикали при подаче
до 20 м3/ч.
Для подачи и распределения смеси непосредственно на
месте укладки в качестве средства вертикального транспорта
(при высоте 2—10 м) применяют хоботы, представляющие
собой трубопровод из конусных металлических звеньев
и верхней воронки. Применяют также виброхоботы,
представляющие собой звеньевой хобот с вибратором.
На загрузочной воронке вместимостью 1,6 м3
и секциях виброхобота диаметром 350 мм через 4-8 м
устанавливают вибраторы-побудители, а также гасители.
Подачу и распределение
бетонной смеси в конструкции на расстоянии до 20 м
с уклоном к горизонту 5-20° обеспечивают виброжелобами
в сочетании с вибропитателем вместимостью
1,6 м3. Им
можно укладывать смеси до 5 м3/ч
при угле наклона 5°, а при угле 15° -до 43 м3/ч.
Качество бетонируемых
конструкций во многом зависит от правильной укладки
и уплотнения бетонной смеси. Смесь при укладке должна
плотно прилегать к опалубке, арматуре и закладным
частям сооружения, а также полностью заполнять (без
каких-либо пустот) объем бетонируемой конструкции.
Способы укладки смеси.
Смесь укладывают горизонтальными слоями толщиной 30-50
см по всей площади бетонируемой части сооружения (блока).
При этом все слои укладывают в одном направлении,
одинаковой толщины, непрерывно на всю высоту и тщательно
уплотняют. Для равномерного распределения смеси в
массивных неармированных блоках применяют малогабаритные
электробульдозеры на базе гусеничного трактора
или оборудованные отвалом электровездеходы,
приводимые в движение питающим электрокабелем. Их
производительность при разравннвании смеси достигает
100 м3/ч (см.
далее рис. 13.7, г). Если размеры бетонируемого блока
не позволяют
Рис. 13.7. Способы укладки бетонной
смеси:
1 — автосамосвал; 2 — автобетоновоз; 3 — автобетоносмеситепь;
4 — вибратор; 5 — упорный брус; в — опалубка;
7 — лоток; 8 — воронка; 9 — труба; 10 — стойка;
11 — виброжелоб (или лоток); 12— вибропитатель;
13— краны; 14 — звеньевой хобот; 15 — самоходные
бетоноукладчики |
применить микробульдозеры, то смесь распределяют вручную
лопатами. Перекидывать смесь во избежание ее расслоения
допускается лишь в исключительных случаях; двойная
перекидка, как правило, не допускается. Продолжительность
укладки слоя ограничивается временем начала схватывания
цемента, устанавливаемого лабораторией. Перекрывать
предыдущий слой последующим необходимо до начала схватывания
цемента в предыдущем слое.
Бетонную смесь лучше всего укладывать из самосвалов,
бетоновозов и бетоносмесителей непосредственно в конструкцию
(рис. 13.7, а—в), т. е. наиболее простым способом.
При невозможности такой укладки смесь в конструкцию
подают с помощью вибропитателя и виброжелобов (рис.
13.7, г). В массивные и больше объемные конструкции
смесь укладывают с помощью специальных бетоновозных
эстакад и передвижных мостов, оборудованных приемными
воронками и хоботами, на которые заезжают бетоновозы.
При бетонировании стен сооружений, в том числе заглубленных
(опускных колодцев и т п ) смесь укладывают кранами
в бадьях (рис. 13.7, д, е) и подъемниками. Укладку
смеси в массивные конструкции, а также в стесненных
условиях осуществляют ленточными транспортерами (конвейерами)
Однако, поскольку при такой укладке много времени
затрачивается на перестановку транспортеров, применять
их целесообразно только . при больших объемах бетона,
укладываемых с одной стоянки. Смесь в рассредоточенные
конструктивные элементы укладывают с помощью самоходных
ленточных бетоноукладчиков со стрелой постоянной длины
(рис. 13.7, ж) и телескопической (рис. 13.7, з).
При необходимости
более интенсивного ведения бетонных работ и частого
перебазирования оборудования применяют автобетононасосы
(АБН), например типа СБ-126, смонтированного на шасси
автомобиля КамАЗ-53213 с распределительной трехсекционной
стрелой длиной 18 м, снабженной бетоноводом диаметром
125 мм АБН можно подавать смесь на расстояние до 400
м и высоту до 80 м. Им особенно удобно подавать смесь
в высокорасположенные (рис 13.8, а) или отдаленные
(рис. 13.8, б) конструктивные элементы при загрузке
смесью из автобетоносмесителей.
Рис. 13.8. Укладка бетонной смеси автобетононасосами:
1 — укладка бетона; 2 - рукав; 3 — шарнирная стрела;
4 - бетоновод; 5 — гидроцилиндр; 6 — авто бетононасос;
7 — приемный бункер; 6 — автобетоносмеситель;
9 — опалубка |
Для бесперегрузочной
укладки смеси используют также пневмонагнетатели (рис.
13.9, а), работающие от компрессора. При необходимости
торкретирования бетонируемого сооружения смесь укладывают
способом пневмонабрызга с помощью компрессора и бетон-шприц-агрегата
(рис. 13.9, в). Однако независимо от применяемого
способа укладки смеси следует обеспечивать неизменность
положения опалубки, арматуры и закладных деталей.
При смещении их следует выправить до затвердения смеси.
Уплотнение
бетонной смеси, необходимое для улучшения
качества и прочности бетонных конструкций, осуществляют
вибрированием или вакуумированием.
При вибрировании
смеси передают колебания, разрушающие силы внутреннего
трения и сцепления между ее частицами В результате
смесь приобретает свойства структурной жидкости, обладающей
текучестью, которая хорошо заполняет опалубочную форму
При этом из смеси удаляется воздух, что также способствует
улучшению структуры и повышению прочности бетона.
Для уплотнения смеси вибрированием применяют вибраторы
различных типов и конструкций (см. п. 6.3). Глубинные
вибраторы выполняются с погруженным в бетонную смесь
и передающим ей колебания вибронаконечником (рис.
13.10, а) или корпусом (рис. 13.10, б). Глубинными
вибраторами смесь уплотняют путем вертикального
или наклонного погружения вибронаконечника или корпуса
в уплотняемый слой. При уплотнении шаг перестановки
глубинного вибратора не должен превышать радиуса его
действия, а глубина погружения в бетонную смесь должна
обеспечивать заглубление его в ранее уложенный слой
на 5-10 см. В процессе уплотнения нельзя касаться
вибратором арматуры, так как это может нарушить ее
сцепление с бетоном. Чтобы не допустить пропущенных
невибрированных участков, смесь уплотняют полосами
вдоль опалубки или арматуры. При бетонировании больших
неармированных блоков, например при устройстве бетонной
подушки крупных опускных колодцев береговых водозаборов,
для уплотнения смеси применяют малогабаритные электротракторы,
оборудованные вибропакетами из четырех подвесных глубинных
вибраторов (см. рис. 13.10, г). Бетонную смесь при
этом подают автобетоновозом и распределяют электротрактором
с отвалом.
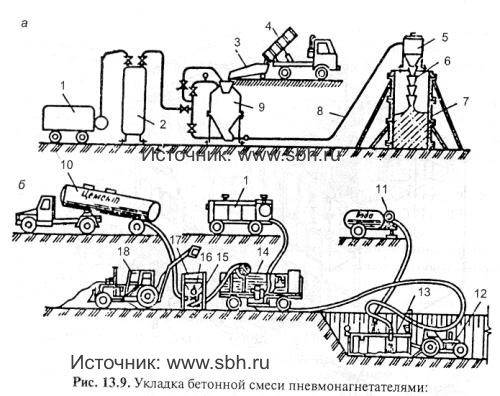
Рис. 13.9. Укладка бетонной смеси пневмонагнетателями:
1 — компрессор; 2 — ресивер; 3 — вибропитатель;
4 — автобетоновоэ; 5 — гаситель; 6 — хобот; 7
— опалубка; 8 —бетоновод; 9 — пневмонагнетатель;
10 — цементовоз; 11 — насос для подачи воды; 72—
трактор; 13— устройство для ведения сопла; 14
— бетон-шприц-агрегат; 15 —дозатор; 16— бункер;
17 — виброгрохот; 18 — экскаватор-бульдозер |
Статья подготовлена и представлена в цифровом виде
компанией "SBH COTPAHC"
Поверхностные
вибраторы, устанавливаемые на уложенную бетонную
смесь, передают ей колебания через рабочую площадку
(см. рис. 13.10, в). Их применяют при уплотнении иеармированных
или армированных одиночной арматурой плоских конструкций
толщиной не более 250 мм, а также с двойной арматурой
толщиной не более 120 мм. Поверхностными вибраторами
смесь уплотняют правильными непрерывными полосами,
перекрывая границы уже провибри-рованного бетона на
10—20 см. Переставляя поверхностный вибратор проволочным
крючком, отрывая его от бетона. Для уплотнения и разравнивания
горизонтальных слоев бетона небольшой толщины (в плитах
днища) наряду с поверхностными вибраторами применяют
вибробрусы (рис. 13.10, д).
Рис. 13.10. Уплотнение бетонной смеси:
а — глубинным вибратором с гибким валом; б — ручным
глубинным вибратором со встроенным электродвигателем;
е — поверхностным вибратором; г — малогабаритным
электротрактором с навесным пакетом вибраторов;
д — вибробрусом; 1 — электродвигатель; 2 — гибкий
вал; 3 — вибронаконечник; 4 — рукоятка; 5 — корпус;
6 — рабочая площадка; 7 — токоподводящий кабель;
8 — шарикоподшипник; 9 — дебаланс; 10— резиновый
амортизатор; П — хомут; 12 — вибраторы ИВ-90;
13 — рама; 14 — электротрактор; 15 — вибробрус;
16 — вибратор |
Вакуумированне
бетона в целях его уплотнения осуществляется
за счет отсоса из смеси свободной, химически не связанной
воды и воздуха. При этом помимо уплотнения смеси уменьшаются
усадочные явления, быстрее нарастает прочность бетона,
повышается морозостойкость и водонепроницаемость.
Прочность вакуумированного бетона по сравнению с вибрированным
выше на 15-20 %. Вакууми-рование бетона производят
с опалубленных и неопалубленных поверхностей. Иногда
также применяют внутреннее вакуумирование с
ломощью погруженных вакуум-трубок. Поскольку вакуумированный
бетон имеет высокую начальную прочность (0,3—0,5 МПа),
во многих случаях можно производить его немедленную
распалубку, а при бетонировании плоских конструкций
приступать к заглаживанию, торкретированию и железнеиию
поверхности. Для вакуумирования применяют жесткие
вакуум-шиты и гибкие вакуумные маты, которые плотно
прижимают к поверхности бетона и герметизируют по
периметру.
Необходимый для
отсоса из бетона воды вакуум создают с помошью агрегатов,
укомплектованных вакуум-насосами или компрессорами.
Процесс вакуумирования заключается в следующем: на
поверхность свежеуложенного бетона укладывают вакуум-щиты,
подключенные через всасываюшие шланги к вакуум-насосу.
При включении его в полости щита образуется вакуум
и из бетона отсасывается воздух и свободная вода.
Производительность вакуум-установки из 20—50 щитов
— 200—250 м2
бетонной поверхности за I цикл вакуумирования. Источник статьи: www.sbh.ru
Поскольку конструкции
обычно бетонируют с перерывами, вызываемыми сменностью
работ, технологическими и организационными причинами,
то место, где после перерыва укладывают свежую бетонную
смесь, называют рабочим швом бетонирования.
Важно правильно выбрать места расположения таких швов
при бетонировании различных конструкций, учитывая
при этом, что контакт и силы сцепления свежеукладываемого
бетона с ранее уложенным и уже твердеющим слабее,
чем в однородном бетоне. В бетонируемых изгибаемых
конструкциях рабочие швы располагают в местах наименьших
значений перерезывающей силы, в колоннах их устраивают
на уровне верха фундамента, у низа прогонов, балок
или подкрановых консолей. Возобновлять бетонирование
в месте шва можно после достижения бетоном у шва прочности
не менее 0,15 МПа, что определяет продолжительность
перерывов до 18-24 ч при температуре воздуха + 15°С.
Поверхность рабочего шва должна быть перпендикулярной
продольной оси элемента, а в стенах и плитах — их
поверхности. При подготовке к бетонированию швы через
8-24 ч после укладки бетона обрабатывают водовоздушной
форсункой или пневмоскребком, а зимой — приводными
стальными щетками. Затем наносят слой цементного раствора
состава 1 : 3, на который укладывают бетонную смесь.
Выдерживание
бетона и уход за ним производят в целях его
твердения, т.е. набора им необходимой прочности. Для
нормального твердения бетона нужна положительная температура
20±2°С с относительной влажностью воздуха не менее
90 %. При нормальных ус ловиях твердения прочность
бетона нарастает довольно быстро, и бетон (на портландцементе)
через 7-14 дней набирает 60-70 % своей 28-дневной
прочности. Затем нарастание прочности замедляется.
Чтобы свежеуложенный бетон приобрел требуемую прочность
в назначенный срок, необходимо: создание влажной среды
при его твердении, предохранение от сотрясений, повреждений
и ударов, резких изменений температуры. Особенно важен
уход за бетоном в первые дни после его укладки, так
как в этот период качество бетона может ухудшиться,
после чего его улучшить практически невозможно. Необходимые
для твердения бетона температурно-влажностные условия
создают укрытием его различными покрытиями, а также
систематической поливкой. Снимать опалубку разрешается
только после приобретения бетоном прочности, установленной
проектом или техническими условиями. Преждевременная
распалубка может привести к повреждению забетонированных
конструкций. Особенно тщательно уход за бетоном организуют
таких конструкций, как стволы водонапорных башен или
оболочки градирен, которые защищают от быстрого высыхания
в течение не менее 14 сут. В теплое время года (не
позднее чем через 5—6 ч после снятия опалубки) открытые
поверхности бетона поливают водой через каждые 3 ч
днем и не реже одного раза ночью в течение 7 сут.,
а затем не реже трех раз в сутки.
5. СПЕЦИАЛЬНЫЕ МЕТОДЫ БЕТОНИРОВАНИЯ
Такие методы бетонирования
применяют в тех случаях, когда обычные методы мало
пригодны или неэкономичны. Из специальных применяют
методы литья, раздельного бетонирования, торкретирования,
инъецирования и др.
Укладка
смеси литьем возможна при применении бетонов
повышенной подвижности, в частности с добавлением
суперпластификаторов, являющихся химическими добавками
(на основе меламиновой смолы или нафталинсульфокислоты).
Введение суиерпластификато-ров в бетонную смесь резко
увеличивает ее подвижность, что, в свою очередь, позволяет
укладывать ее в опалубку методом литья, т.е. без необходимости
ее распределения и виброуплотнения. При этом смесь
полностью заполняет всю опалубку под действием гравитационных
сил. Метод позволяет сократить расход цемента и повысить
качество бетонируемых конструкций.
Метод
раздельного бетонирования заключается в раздельной
укладке в опалубку крупного заполнителя (щебня), а
затем цементно-
песчаного раствора, который заполняет в нем пустоты.
Его применяют при возведении железобетонных резервуаров,
бетонировании в условиях интенсивного притока грунтовых
вод и в других случаях.
Раздельное бетонирование
может быть гравитационным и инъекционным.
При первом раствор проникает в крупный заполнитель
под действием сил тяжести, а при втором - под давлением,
создаваемым нагнетателем. Метод нагнетания раствора
более эффективен и может быть применен для бетонирования
тонкостенных конструкций. Гравитационное раздельное
бетонирование с заливкой раствора сверху применяют
при бетонировании конструкций высотой до 1,2 м, а
при большей высоте их - инъекционное, с нагнетанием
раствора через трубы-инъекторы. При толщине конструкции
более 1 м раствор нагнетают через стальные трубы,
устанавливаемые в опалубку, а при толщине менее 1
м - через боковые инъекционные отверстия. Для нагнетания
раствора применяют растворо-насосы. Время бетонирования
яруса не должно превышать продолжительности схватывания
цемента в растворе. Нагнетают раствор непрерывно снизу
вверх под давлением 0,15-0,2 МПа и по мере нагнетания
трубы поднимают. Перерывы в производстве работ более
20 мин не допускаются, так как может произойти закупорка
инъекционных труб.
При использовании
данного метода уменьшается объем работ по перемешиванию
материалов, упрощается технологическая схема работ,
исключаются рабочие швы бетонирования, что увеличивает
монолитность конструкций. К недостаткам относится
необходимость применения растворов с высоким содержанием
цемента. Однако этот недостаток может быть устранен
при использовании метода вибронагнетания,
когда одновременно с нагнетанием раствора осуществляется
его глубинное вибрирование.
Торкретирование
заключается в последовательном нанесении на обрабатываемую
бетонную поверхность слоев цементно-песчаного раствора
(торкрета) с помощью цемент-пушки или бетонной смеси
(набрызг-бетон) с помощью бетон-шприц-машины (см.
рис. 13.9, б). Торкретирование применяют для повышения
водонепроницаемости железобетонных емкостных сооружений,
а также бетонирования тонкостенных конструкций в тех
случаях, когда обычные способы бетонирования сложны
или не обеспечивают нужной плотности бетона. Методом
торкретирования исправляют дефекты в бетонных и железобетонных
конструкциях.
Торкретирование с помощью цемент-пушки или набрызг-бетони-рование
бетон-шприц-машиной ведут следующим образом. Сухую
цементно-песчаную или бетонную смесь из резервуара
под давлением воздуха подают по шлангу к наконечнику,
где, смешивая ее с водой, наносят на поверхность бетона
или арматурную сетку.
Инъецирование
(заполнение) каналов и заполнение пазов предварительно
напряженных конструкций. Пустоты в каналах предварительно
напряженных конструкций заполняют цементным раствором,
чтобы защитить натянутую арматуру от коррозии и одновременно
обеспечить ее сцепление с бетоном конструкций. К инъецированию
каналов приступают сразу после натяжения арматуры.
Для инъеци-рования готовят раствор на цементе марок
400-500, который подают в канал растворонасосом. Инъецирование
ведут непрерывно под давлением 0,6-0,8 МПа до тех
пор, пока раствор не начнет выходить с другой стороны
канала. Пазы после навивки кольцевой напряженной арматуры
на стены цилиндрических емкостных сооружений заполняют
торкретным покрытием, наносимым на поверхность стен
цемент-пушкой методом «снизу вверх» после гидравлического
испытания емкости.
6. ПОДВОДНОЕ БЕТОНИРОВАНИЕ
Методы
подводного бетонирования применяют для возведения
подводных частей сооружений, например затопленных
оголовков русловых водозаборов, днищ их опускных колодцев
и насосных станций (при погружении без водоотлива),
а также при их ремонте и восстановлении. Подводное
бетонирование выполняют различными методами, в том
числе методом вертикально перемещающейся трубы (ВПТ),
восходящего раствора (ВР), укладкой бункерами, утрамбовы-ванием
бетонной смеси, укладкой в мешках.
Подводное
бетонирование методом ВПТ заключается в непрерывной
подаче бетонной смеси по опущенной сквозь толщу воды
и погруженной в смесь на дно трубе в условиях, исключающих
вымывание цемента. Только верхний слой первой порции
бетонной смеси соприкасается с водой, остальная смесь,
поступающая через нижнее отверстие трубы, остается
защищенной верхним слоем от контакта с водой (рис.
13.11, а, 6). Бетонирование этим методом можно производить
при глубине воды до 50 м и толщине укладываемого слоя
бетона не менее 1 м. Подводную конструкцию (блок,
захватку) методом ВПТ бетонируют непрерывно до уровня,
превышающего проектную отметку на величину, равную
2% высоты конструкции, но не менее чем 20 см.
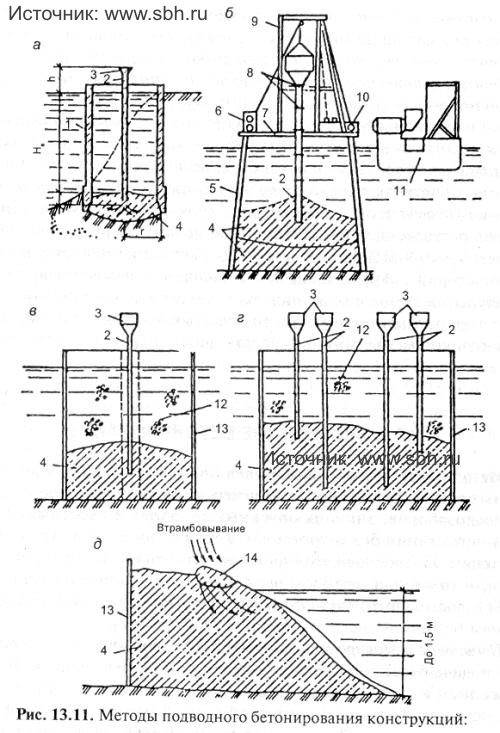
Рис. 13.11. Методы подводного бетонирования
конструкций:
а — укладка бетонной смеси способом ВПТ (в подушку
опускного колодца); б— бетонирование способом
ВПТ с плавучим бетонным заводом; в — бетонирование
способом ВР с шахтой; г — то же, без шахты; д
— бетонирование способом утрамбования бетонной
смеси; 1 — опускной колодец; 2 —- заливочные трубы;
3 — воронка; 4 — свежеуложенная и уложенная бетонная
смесь; 5 — бездонный железобетонный ящик; 6 —
лебедка; 7 — рабочая площадка; 8 — соединение
звеньев трубы; 9 — башенный подъемник; 10 — загрузочный
ковш подъемника; 11 — плавучий бетонный завод;
12— крупный заполнитель; 13— опалубка; 14 — новая
порция бетонной смеси |
Бетонирование
методом восходящего раствора (ВР), или методом
раздельного бетонирования, осуществляется путем
подачи цементного раствора в опалубленную подводную
стену (или массив — блок), предварительно загруженную
крупным заполнителем. При этом бетонирование может
выполняться различными видами этого метода, в том
числе: безнапорное (гравитационное) бетонирование,
когда заливочные трубы устанавливают в решетчатых
ограждающих шахтах и распространение раствора в пустоты
крупного заполнителя происходит под действием массы
раствора (рис. 13.11, в); напорное бетонирование
(инъекционный метод), когда установленные в блоке
трубы засыпаются крупным заполнителем и распространение
раствора обеспечивается давлением, создаваемым массой
столба раствора в трубах или растворонасосом (рис.
13.11, г); напорное бетонирование с вибрацией
(вибронагнетательный метод), когда распространение
раствора в пустотах заполнителя обеспечивается давлением,
создаваемым растворонасосом, и воздействием вибраторов,
устанавливаемых отдельно от заливочных труб на расстоянии,
не превышающем радиуса действия этих труб.
Бетонирование
укладкой бетона бункерам (бадьями, ящиками, грейферами)
выполняют путем опускания их под водой на основание
опускаемого блока или ранее уложенный слой бетона
и последующим выпусканием бетонной смеси через раскрывающееся
дно или затвор.
Бетонирование
методом втрамбовывания бетонной смеси применяют
при глубине воды до 1,5 м. Бетон укладывают с берега
от уреза воды или с бетонного островка, причем последующие
порции смеси укладывают и утрамбовывают в ранее уложенные,
но еще не схватившиеся (рис. 13.11, д). Таким образом,
с водой соприкасается только бетон, а утрамбовываемая
смесь остается изолированной от воздействия воды.
Для укладки бетона в мешках применяют мешки, на 2/3
заполненные бетонной смесью. Работы выполняют водолазы,
которые укладывают мешки вперевязку.
Статья подготовлена и представлена в цифровом виде
компанией "SBH COTPAHC"
7. ОСОБЕННОСТИ ПРОИЗВОДСТВА
БЕТОННЫХ РАБОТ НА МОРОЗЕ И В УСЛОВИЯХ ЖАРКОГО КЛИМАТА
Главной особенностью
и требованием при зимнем бетонировании является создание
такого режима укладки и твердения бетона, при котором
он к моменту замерзания приобретает необходимую прочность,
называемую критической. Пределы такой прочности
указаны в СНиПе, в частности, для бетона марки М150
она должна составлять не менее 50% проектной, для
марок М200-М300 - 40 %, но независимо от марки 70
% — для конструкций, подвергающихся по окончании выдерживания
замораживанию и оттаиванию, 80 % — для предварительно
напряженных конструкций и 100 % — для конструкций,
подвергающихся сразу после выдерживания действию расчетной
нагрузки (давлению воды и др.).
Способы
укладки бетона зимой в значительной мере
определяются применяемыми способами его выдерживания.
На практике применяют как безобогревные способы выдерживания
(способ термоса и термоса с добавками - ускорителями
твердения, противоморозны-ми добавками), так и способы
искусственного подогрева или прогрева конструкций
(электротермообработка бетона, применение греющей
опалубки и покрытий, обогрев паром, горячим воздухом
или в тепляках).
Выдерживание
бетона способом термоса применяется для массивных
конструкций. Массивность конструкций характеризуется
отношением суммы охлаждаемых наружных поверхностей
к ее объему, называемым модулем поверхности
(Мп). Способом
термоса выдерживают конструкции с модулем поверхности
до 6. Способ основан на использовании: утепленной
опалубки, тепла подогретых составляющих смеси, а также
тепла, выделяемого в процессе схватывания и твердения
цемента вследствие экзотермии. При этом хорошо укрытый
бетон остывает настолько медленно, что успевает набрать
критическую прочность до замерзания. При данном способе
применяют быстротвердеющие портландцементы, а также
портландцементы высоких марок (не ниже 400), которые
не только быстро набирают прочность, но и выделяют
при твердении значительное количество воды.
Применение
противоморозных добавок (хлорида натрия в
сочетании с хлоридом кальция, нитрата натрия, поташа
и др.) в количестве 3— 16 % от массы цемента, обеспечивающих
твердение при отрицательных температурах, позволяет
транспортировать бетонную смесь в неутепленной таре
и укладывать ее на морозе. При выборе вида добавки
учитывают область применения бетонов с химическими
добавками и имеющиеся ограничения. Оптимальное количество
добавок обычно не превышает 16% от массы цемента.
Смесь с противоморозными добавками укладывают в конструкции
и уплотняют с соблюдением общих правил укладки бетона.
Электротермообработка
бетона основана на использовании тепла, получаемого
от превращения электрической энергии в тепловую. Электротермообработку
осуществляют методами электродного прогрева (электропрогрева),
а также путем электрообогрева различными электронагревательными
устройствами, индукционного нагрева (в электромагнитном
поле). Электродный прогрев бетона обеспечивается через
электроды, располагаемые внутри или на поверхности
бетона. Соседние или противоположные электроды подсоединяют
к проводам разных фаз, в результате чего между электродами
в бетоне возникает электрическое поле, прогревая его.
Ток в армированных конструкциях пропускают напряжением
50-120 В, а в неармированных - 127-380 В. При прохождении
тока бетон нагревается и в течение 1,5-2 сут. приобретает
распалубочную прочность.
Электрообогрев
бетона осуществляют инфракрасными лучами, передающими
теплоту в виде лучистой энергии, используя в качестве
источников таких лучей трубчатые электронагреватели
(ТЭНы) и стержневые карборундовые излучатели. Используют
также контактный электрообогрев путем непосредственной
передачи теплоты от нагревающих поверхностей к прогреваемому
бетону. Его используют в греющих подъемно-переставной
и разборно-щитовой инвентарной опалубках. Бетонные
подготовки и дниша, например, емкостных сооружений
(резервуаров и др.) толщиной до 20 см бетонируют с
прогревом полосовыми электродами, закрепленными на
накладных деревянных щитах (рис. 13.12, а), с подключением
их к трем фазам электросети. Электрообогрев можно
выполнять с помощью различных нагревателей — проволочных,
греющих кабелей и проводов, стержневых, трубчатых,
сетчатых, пластинчатых и др.
Индукционный
прогрев осуществляют за счет преобразования энергии
переменного магнитного поля в арматуре или стальной
опалубке в тепловую с передачей ее бетону с помощью
индукционной обмотки.
Обогрев
бетона в греющей опалубке и покрытиях. Греющую
(термоактивную) опалубку (см. рис. 13.2, ж) применяют
для обогрева тонкостенных и среднемассивных конструкций
(с любой степенью армирования) при температурах наружного
воздуха до -40°С. Для обогрева конструкций типа днищ
емкостных сооружений применяют инвентарные термоактивные
гибкие покрытия (ТАГП): сборно-разборное (см. рис.
13.12, б), цельноклееное (рис. 13.12, в), с греющим
проводом (рис. 13.12, г). При скоростном возведении
вертикальных стен, например, водонапорных башен, градирен
в скользящей опалубке применяют двухсторонний их обогрев
с установкой термоактивного подвесного покрытия (ТАПП)
(рис. 13.12, д).
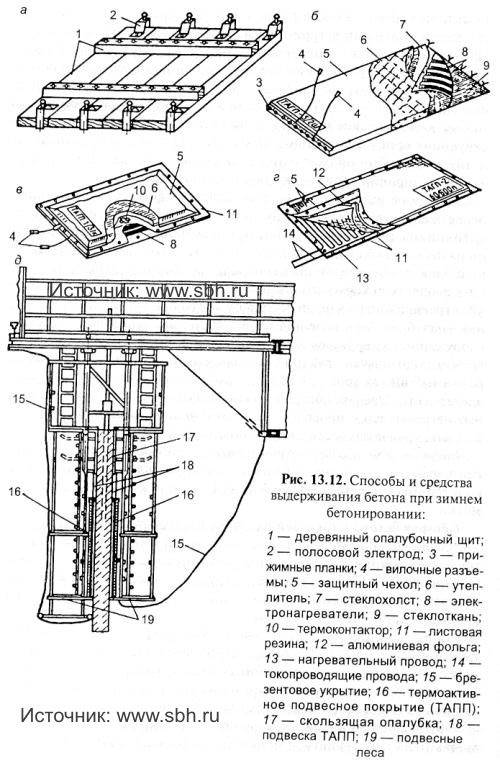
Рис. 13.12. Способы и средства выдерживания
бетона при зимнем бетонировании:
1 — деревянный опалубочный щит; 2— полосовой электрод;
3— прижимные планки; 4 — вилочные разъемы; 5 —
защитный чехол; 6 — утеплитель; 7 — стекпохолст;
8 — электронагреватели; 9 — стеклоткань; 10 —
терм о контактор; 11 —листовая резина; 12— алюминиевая
фольга; 13 — нэгревательный провод; 14 — токо
про водящие провода; 15 — брезентовое укрытие;
16 — термоактивное подвесное покрытие (ТДПП);
77— скользящая опалубка; 18 — подвеска ТАПП; 19—
подвесные леса |
Обогрев
бетона паром или горячим воздухом. Обогрев
паром применяют для конструкций с модулем поверхности
больше 8-10. Этот способ прогрева обеспечивает благоприятные
тепловлажностные условия для твердения бетона, однако
требуется большой расход пара (до 2 т на 1 м3 бетона),
а также устройство паровых рубашек, трубопроводов
и т.п. Применяют следующие разновидности паропрогрева:
прогрев в паровой рубашке, при котором пар подается
в замкнутое пространство, образованное вокруг прогреваемой
конструкции паронепроницаемым ограждением, отстоящим
от опалубки на 10-15 см. Этот метод эффективен для
конструкций с большими поверхностями.
Применение
тепляков, или шатров, создающих замкнутое
пространство, внутри которого бетонируют и выдерживают
конструкции в естественных условиях (без подогрева
воздуха), не получило широкого практического распространения,
а использование пленочных тепляков шатрового типа
с подогревом воздуха внутри них является эффективным
и прогрессивным способом зимнего бетонирования.
Технология
бетонных работ в условиях сухого жаркого климата имеет
ряд особенностей. Такие сложные климатические условия
наступают при летней температуре наружного воздуха
35-40°С при относительной влажности 10-25%, интенсивной
солнечной радиации и частых ветрах. Совокупное воздействие
таких факторов приводит к быстрому обезвоживанию (высушиванию)
бетона, что замедляет и даже прекращает процессы гидратации
цемента. Вследствие быстрого высушивания бетона прочность
его снижается почти на 50% по сравнению с бетоном,
твердеющим в нормальных температурно-влажностных условиях.
Поэтому,
чтобы обеспечить надлежащее качество бетонных и железобетонных
конструкций водопроводных сооружений, возводимых в
условиях сухого жаркого климата, необходимо применять
такие методы приготовления, транспортирования, укладки
и ухода за бетоном, которые бы препятствовали или
сводили к минимуму его обезвоживание.
Так,
при приготовлении смеси необходимо применять меры,
обеспечивающие сохранение требуемой консистенции смеси
к моменту ее укладки в опалубку. Этого можно достичь,
в частности, за счет снижения температуры смеси в
процессе ее приготовления, а также принятия мер против
обезвоживания смеси при ее транспортировании, укладке
и выдерживании при твердении бетона. Существенно снизить
температуру смеси (до 20°С) при температуре наружного
воздуха до 40°С и низкой относительной влажности можно
путем смачивания охлажденной водой заполнителей и
обдува холодным воздухом при подаче их в смеситель
и т.д. С этой же целью иногда добавляют в воду затворения
до 50 % льда (к ее массе).
Чтобы сохранить
требуемую консистенцию смеси, в нее полезно вводить
поверхностно-активные добавки (0,4-0,5 % массы цемента).
В условиях сухого и жаркого климата следует увеличивать
продолжительность перемешивания бетонной смеси на
30-50 %. При этом соблюдают такой порядок: вначале
в бетоносмеситель загружают заполнитель, а также 2/3
расчетного количества воды и перемешивают в течение
1-2 мин. Затем добавляют цемент, остальную воду, вводят
добавки и вновь перемешивают 3-4 мин.
Готовую бетонную
смесь к месту укладки следует транспортировать в закрытой
таре. Для этих целей наиболее подходят автобетоновозы
и автобетоносмесители.
При транспортировании
смеси необходимо избегать дальних перевозок, так как
при этом она обезвоживается и теряет свою подвижность.
В целом, в условиях
сухого и жаркого климата наиболее эффективна следующая
технологическая схема: загрузка смеси на бетонном
заводе в автобетоносмеситель, перевозка ее в сухом
виде к месту укладки, добавление воды и перемешивание
в автобетоносмесителе непосредственно у места бетонирования
и немедленная укладка смеси в конструкции.
Перед укладкой
смеси внутреннюю поверхность опалубки следует увлажнять.
Формирующую поверхность опалубки из влагопогло-щающих
материалов (дерева, фанеры) надо покрывать специальными
составами или полимерными пленками, предотвращающими
сцепление с бетоном, а также поглощение воды из него.
При подаче и распределении
бетонной смеси необходимо избегать многократную ее
перегрузку и быстрого ее обезвоживания. Исходя из
этого, не следует подавать смесь в открытых транспортерах,
а также длинными лотками и виброжелобами. Более целесообразна
подача смеси бетононасосами по трубам или краном в
бадьях большой емкости. При этом свободное падение
смеси не должно превышать 1,5-2 м.
Процесс бетонирования
желательно вести непрерывно.
Важное значение
при бетонировании в условиях сухого и жаркого климата
имеет своевременный и тщательный уход за бетоном.
С этой целью открытые поверхности свежеуложенного
бетона надо покрывать мешковиной, рогожами, брезентом;
после укладки бетон через каждые 3-4 часа надо увлажнять.
Там, где имеются
условия, например, при бетонировании подготовки или
днища емкостных сооружений, их заливают водой через
6—12 ч после укладки смеси.
Однако, учитывая
часто наблюдаемый дефицит источников воды в районах
с сухим и жарким климатом, целесообразно применять
так называемые «сухие» безвлажностные методы ухода
за бетоном, в том числе твердение бетона под специальными,
воздухонепроницаемыми навесами из пленки или посредством
покрытия поверхности бетона различными составами.
Конструкции небольших размеров можно сразу же после
бетонирования накрывать легкими переносными шатрами
из полихлорвиниловой пленки на каркасе из стальных
трубок или стержней диаметром 16-20 мм. В этом случае
при необходимой герметичности устройства внутри его
создаются условия, близкие к мягкому режиму пропаривания.
Обезвоживание бетона можно также значительно снизить
за счет ускорения его твердения, для чего следует
применять высокоактивные, но мало усадочные цементы,
ускорители твердения, а также методы тепловой обработки,
в том числе при помощи герметичных пленочных навесов.
8. ТРЕБОВАНИЯ К КАЧЕСТВУ
БЕТОННЫХ РАБОТ
Качество
бетонных и железобетонных конструкций зависит от качества
используемых материалов, а также от соблюдения основных
требований технологии на всех стадиях комплексного
процесса бетонных работ.
Для
этого необходим контроль на всех стадиях этих работ,
включая: приемку и хранение исходных материалов (цемента,
песка, щебня, арматурной стали, лесоматериалов и др.);
изготовление и монтаж арматурных сеток и каркасов,
изготовление и монтаж опалубки; подготовку основания
и опалубки к укладке бетонной смеси; приготовление
и транспортировку смеси; укладку, уплотнение и уход
за бетоном в процессе его твердения.
Все
исходные материалы должны отвечать требованиям ГОСТа.
Показатели свойств материалов следует проверять в
строительной лаборатории по принятой единой методике.
На
стадии приготовления смеси проверяют точность дозировки
материалов, продолжительность перемешивания, подвижность
и плотность смеси. Причем подвижность надо проверять
не реже двух раз в смену, и она не должна от заданной
более чем на 1 см, а плоьность - более чем на 3%.
При транспортировке
смеси следят за тем, чтобы она не начала схватываться,
не расслаивалась на составляющие, не теряла подвижности
из-за потерь воды, цемента или схватывания.
В процессе армирования
проверяют качество арматурной стали, правильность
формы и размеров (диаметров) стержней, качество сварки,
правильность положения арматуры в конструкции с учетом
допускаемых отклонений, приведенных в СНиПе. Аналогично
при устройстве опалубки особое внимание надо обратить
на правильность ее установки, плотность стыков в щитах
и сопряжениях, взаимное положение опалубочных форм
и арматуры (для обеспечения необходимого защитного
слоя бетона).
Перед укладкой
бетонной смеси проверяют чистоту поверхности опалубки
и качество ее смазки. Контролируют в процессе укладки
смеси высоту ее сбрасывания, продолжительность вибрирования
и равномерность уплотнения, не допуская расслоения
смеси и образования раковин, пустот.
Процесс виброуплотнения
контролируют визуально, по степени осадки смеси, прекращению
выхода из нее пузырьков воздуха и появлению на поверхности
цементного молока. В некоторых случаях используют
плотномеры.
Контроль
качества уложенного бетона осуществляют систематически
в процессе бетонирования конструкций. Он заключается
в проверке соответствия физико-механических характеристик
бетона требованиям проекта. Прочность бетона на сжатие
проверяют на контрольных образцах, изготовленных из
бетонной смеси, взятой после ее приготовления и непосредственно
на месте укладки. Приемку выполненных монолитных бетонных
и железобетонных конструкций производят лишь после
достижения бетоном проектной прочности. Железобетонные
резервуары и другие емкостные сооружения испытывают,
кроме того, на утечку воды из них, а метантенки -
на утечку воздуха.
Особые меры контроля
качества применяют при выполнении бетонных работ в
зимнее время. Так, в процессе приготовления смеси
через каждые 2 ч проверяют: отсутствие льда, смерзшихся
комьев в необогреваемых заполнителях, подаваемых в
бетоносмеситель, при приготовлении смеси с противоморозными
добавками, температуру воды и заполнителей перед загрузкой;
концентрацию солей; температуру смеси на выходе из
бетоносмесителя. При транспортировании смеси один
раз в смену проверяют выполнение мер укрытия, утепления
и обогрева транспортной и приемной тары. Если смесь
подвергают предварительному электроразогреву, то контролируют
ее температуру в каждой разогреваемой порции.
При укладке смеси
следят, чтобы не было снега и наледей на поверхности
основания, арматуры и опалубки, следят за соответствием
теплоизоляции опалубки, а при необходимости отогрева
- за выполнением этих работ. Температуру смеси проверяют
во время выгрузки смеси из транспортных средств и
непосредственно после укладки в опалубку. Источник статьи: www.sbh.ru
В процессе выдерживания
бетона его температуру измеряют дистанционными методами
с использованием температурных скважин, термометров
сопротивления либо технических термометров, причем,
если используется способ «термоса», предварительного
электроразогрева смеси или обогрева в тепляках, температуру
бетона измеряют каждые 2 ч в первые сутки и не реже
двух раз в смену в последующие трое суток и один раз
в остальное время выдерживания. В случае применения
бетонов с противоморозными добавками температуру его
проверяют три раза в сутки до приобретения им заданной
прочности, а при электропрогреве бетона в период подъема
температуры со скоростью до 10°С/ч — через каждые
два часа, в дальнейшем — не реже двух раз в смену.
Прочность бетона
контролируют путем испытания дополнительного количества
образцов, изготовленных у места укладки бетонной смеси
при соблюдении сроков, предусмотренных для различных
способов зимнего бетонирования и указанных в инструкциях
и справочниках. Образцы, хранящиеся на морозе, перед
испытанием выдерживают 2—4 ч для оттаивания при температуре
15—20°С.
9. ОСНОВНЫЕ ТРЕБОВАНИЯ
ОХРАНЫ ТРУДА ПРИ ПРОИЗВОДСТВЕ БЕТОННЫХ И ЖЕЛЕЗОБЕТОННЫХ
РАБОТ
При установке
опалубки
в несколько ярусов каждый последующий ярус устанавливают
только после закрепления нижнего. Разбирать опалубку
после достижения бетонов заданной прочности можно
с разрешения производителя работ. Заготавливать и
обрабатывать арматуру необходимо в специально предназначенных
для этого и соответственно оборудованных мастерских
или цехах. При выполнении работ по натяжению арматуры
в местах прохода работающих необходимо установить
защитные ограждения высотой не менее 1,8 м. Монтаж,
демонтаж и ремонт бетоноводов, а также удаление из
них пробок бетона допускаются только после снижения
давления до атмосферного. Ежедневно перед началом
укладки бетона в опалубку необходимо проверять состояние
ее и подмостей
и в случае обнаружения неисправностей их следует незамедлительно
устранить. Рабочие, укладываюшие бетонную смесь на
поверхности, имеющей уклон более 20° (конусные днища
отстойников), должны пользоваться предохранительными
поясам. При уплотнении смеси электровибраторами перемешать
их за токоподводящие шланги не допускается, а при
перерывах в работе и переходах с одного места на другое
вибраторы следует выключать. Зона электропрогрева
бетона должна быть ограждена, иметь световую сигнализацию
и знаки безопасности. Пребывание людей и выполнение
ими каких-либо работ в этой зоне без соответствующих
средств защиты не допускается.
Статья подготовлена и представлена в цифровом виде
компанией "SBH COTPAHC"
|